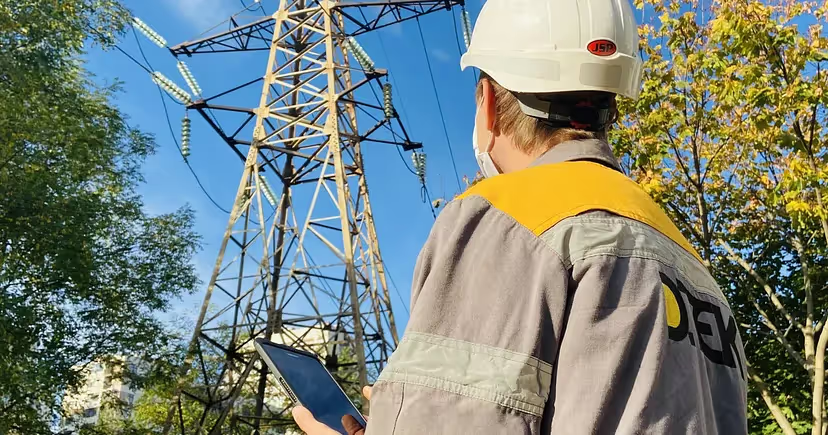
Today, the time of reaction and response speed of mobile crews is a decisive factor in quickly restoring damaged networks and equipment. Suppose specialists can optimize resource use and minimize the time needed to eliminate malfunctions or carry out planned works. In that case, it will significantly speed up the restoration of electricity and heating in Ukrainian homes. With this initiative, DTEK, the largest energy holding, turned to MODUS X to implement the solution for three business directions, which will ensure continuous processes of automation and optimization of the tasks of mobile repair and inspection crews.
Today, the time of reaction and response speed of mobile crews is a decisive factor in quickly restoring damaged networks and equipment. Suppose specialists can optimize resource use and minimize the time needed to eliminate malfunctions or carry out planned works. In that case, it will significantly speed up the restoration of electricity and heating in Ukrainian homes. With this initiative, DTEK, the largest energy holding, turned to MODUS X to implement the solution for three business directions, which will ensure continuous processes of automation and optimization of the tasks of mobile repair and inspection crews.
Since employees working at different locations are involved in the process, and the route of mobile crews usually consists of several locations (warehouse, facility), the solution must ease the most optimal way of utilizing resources and practical cooperation between divisions.
MODUS X proposed digitizing the operational activities of the crews by creating a unified application — a comprehensive solution that integrates mobile and web applications with the enterprise resource planning software SAP S4/HANA and the corporate storage Microsoft SharePoint, working in combination with SAP Connector for secure data transmission. This solution allows for the automation of planning, accounting of works, and materials write-off, thereby increasing efficiency and reducing the time for eliminating accidents or carrying out planned works.
The need to create a mobile application arose due to the necessity to optimize and automate the processes of planning, managing, and operational coordination between repair and inspection crews, remote employees, and dispatchers. Brigades, going out to locations for planned or emergency works, faced a lack of a precise task distribution mechanism and spent a lot of time on documentation and filling out forms on paper, leading to significant operational complications and delays in restoring the operation of electric network sections or equipment at substations.
DTEK aimed to optimize this entire process and make it as transparent and efficient as possible regarding resource use.
“We immersed ourselves in the previously set up processes, actively listened and analyzed needs, and found the solution that became the perfect bridge between technologies and real business tasks. Such an approach allowed us to create not just an application but a truly individual solution that adapts to the needs of a specific business,” comments Alesia Komarova, Product Manager at MODUS X.
The solution implemented by MODUS X for DTEK covers the process of communication and interaction between different divisions during planned repair works and emergencies, digitizing all paper operational processes. The process can be divided into five key stages:
Moreover, the solution allows for controlling the location of employees and facilities, optimizing routes and work duration. Integrated with business systems like SAP S4/HANA and Microsoft SharePoint, the solution enables planning and task setting, accounting for work completion, and materials write-off from a single interface.
“The digital solution allows integration with the company’s accounting systems, providing control over the accident elimination process in real-time and optimal resource planning,” says Alex Vygodski, Head of Enterprise Applications and Technologies at MODUS X. “The digital product consists of mobile and web applications, as well as an integration component, SAP Connector.”
Overall, the digital product consists of the following components:
Using SAP MRS for short-term planning and mobile devices for recording works increases productivity and ensures transparency of work execution.
Implementing the solution allowed DTEK to optimize the process of eliminating damage on electric networks and substations, reduce the time for maintenance and emergency response, significantly decrease paper documentation, ensure transparency of completed works, and increase overall customer satisfaction by reducing the duration of power outages.
“Thanks to the new IT solution, our employees can eliminate accidents 15% faster on average. The need for paper orders and agreements is eliminated. Repair crews do not need to call the dispatcher again. It is enough to mark the start of works in the mobile application and record the fact of their completion,” comments Denys Bondar, CEO of DTEK Kyiv Grids.
The energy-holding DTEK does not stop at the results achieved, and together with MODUS X, it confidently continues the path to the digital transformation of the company group’s operational processes.